Het beschermen van medische producten tegen besmetting en het handhaven van constante omgevingscondities zijn essentieel in de farmaceutische industrie. Net als bij de uitbreiding van de Portugese fabriek in 2016 vertrouwde Fresenius Kabi ook voor de nieuwe productiefaciliteit op de rookarme isolatiematerialen van Armacell. ArmaFlex Ultima is gebaseerd op de gepatenteerde ArmaPrene® technologie en genereert bij brand 10 keer minder rook dan een standaard elastomeer product, waardoor het de veiligste oplossing is voor koelsystemen.
Uitbreiding van een ultramoderne productiefaciliteit
Fresenius Kabi is een internationaal actieve onderneming in de gezondheidszorg en is gespecialiseerd in de ontwikkeling en levering van geneesmiddelen, medische technologie voor infuus- en transfusietoepassingen en klinische voeding. De Portugese dochteronderneming Labesfal S.A., gevestigd in Santiago de Besteiros, is een van de vijf grootste producenten van generieke geneesmiddelen in Portugal. Labesfal produceert capsules, tabletten, vloeibare geneesmiddelen en steriele farmaceutische poeders. De locatie beslaat bijna 100.000 vierkante meter en herbergt gebouwen met onafhankelijke productieruimten en logistieke en opslagruimten. Er zijn ook gebouwen voor kwaliteitscontrole en administratieve activiteiten op de site.
In 2016 investeerde het bedrijf in een nieuwe fabriek voor de productie van penicilline en in 2021 breidde het zijn industriële complex verder uit met een nieuwe menginstallatie van 6.000 m² voor de productie van parenterale voeding. Deze nieuwe faciliteit is ontworpen voor een reeks processen om voedingsformuleringen voor pediatrische en volwassen patiënten te produceren.
GMP waarborgt de productie in de farmaceutische industrie
Kwaliteitsborging is een topprioriteit in de farmaceutische industrie, omdat kwaliteitsafwijkingen een directe impact kunnen hebben op de gezondheid van patiënten. Een hoge productkwaliteit wordt gegarandeerd door strikte naleving van de huidige GMP-normen (current Good Manufacturing Practice). Deze normen definiëren richtlijnen voor de kwaliteitsborging van productieprocessen en -omgevingen bij de productie van geneesmiddelen. Een van de belangrijkste doelstellingen van de GMP-regels is het voorkomen van elke vorm van verontreiniging tijdens de productie. Dit geldt natuurlijk ook voor de materiaalkeuze bij het ontwerpen van nieuwe productiefaciliteiten.
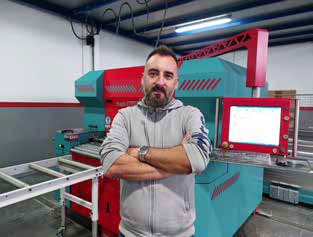
Hoge eisen aan de gebruikte isolatiematerialen
“De belangrijkste vereisten voor de technische isolatie in het Labesfal-project waren een goed brandgedrag en de afwezigheid van vezels. Vezels zijn uit den boze in deze cleanroomomgeving, omdat vrije deeltjes de lucht zouden kunnen verontreinigen. Daarom werd ArmaFlex Ultima gekozen, omdat dit materiaal volledig aan de eisen voldeed. Het materiaal met gesloten cellen geeft geen stof of vezels af en heeft een hoge weerstand tegen waterdampdiffusie om langdurige bescherming tegen condensatie te garanderen en energieverlies te voorkomen. Het is ook zeer flexibel en eenvoudig te installeren.”
Basilio Oliveira, eigenaar en directeur van Martins Oliveira, Lda (Portugal)
Schone ruimtetechnologie
Het bouwproject werd gepland en gerealiseerd in overeenstemming met de nieuwste en hoogste Europese kwaliteitsnormen. De cleanroomtechnologie zorgt voor constant schone omgevingscondities dankzij gefilterde lucht. Een belangrijke maatregel voor het minimaliseren van deeltjesbesmetting is het genereren van een laminaire, deeltjesvrije luchtstroom. Temperatuur, vochtigheid en druk moeten te allen tijde op een constant niveau worden gehouden.
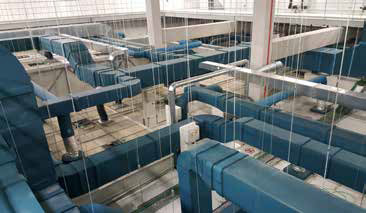
Enorme koelbehoefte
Met buitentemperaturen tot 33 °C in de zomer en een relatieve vochtigheid tot 80 procent in de winter heeft de fabriek in Labesfal een aanzienlijke behoefte aan airconditioning. Enorme koelunits met een koelvermogen van 600 kW voorzien de nieuwe fabriek van gekoelde lucht.Net als bij de uitbreiding van de fabriek in 2016 vertrouwde Labesfal opnieuw op ArmaFlex Ultima om de systemen te isoleren. Het ingenieursbureau Indus Ingenieria y Arquitectura (Barcelona) schreef een aanbesteding uit voor het hoogwaardige materiaal voor de isolatie van luchtbehandelingskanalen en koelsystemen.
Vezel- en stofvrije isolatie voor hygiënische productie
Om elke vorm van besmetting te voorkomen die een negatieve invloed zou kunnen hebben op het eindproduct, moeten isolatiematerialen in cleanroomomgevingen vrij zijn van stof en vezels.Stof en vezels kunnen niet alleen een steriele productie in gevaar brengen, samen met vocht vormen ze ook een ideale voedingsbodem voor de groei van bacteriën en schimmels. Flexibele elastomere isolatiematerialen bestaan uit een homogeen materiaal met gesloten cellen en een glad oppervlak. De gesloten microcelstructuur zorgt voor een hoge weerstand tegen waterdampdiffusie “ingebouwd” in het materiaal en een hoge weerstand tegen vochtopname uit de omgevingslucht. Deze homogene, driedimensionaal vernette structuur voorkomt vervuiling van de lucht met isolatiedeeltjes, vezels, stof, microben en andere elementen die kunnen bijdragen aan luchtvervuiling. Het gladde oppervlak is eenvoudig stofvrij en schoon te houden. ArmaFlex producten bieden passieve bescherming tegen micro-organismen omdat het moeilijk is voor ziekteverwekkers om zich te hechten aan het gladde en niet-poreuze oppervlak van het materiaal, waar ze niet de voedingsstoffen kunnen vinden die ze nodig hebben om te groeien. Het isolatiemateriaal met gesloten cellen beschermt technische systemen op betrouwbare wijze tegen condensatie op lange termijn.
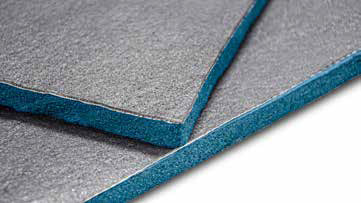
Rook is de grootste bron van gevaar bij brand
Naast de materiaaleigenschappen is ook het brandgedrag van de gebruikte bouwmaterialen van cruciaal belang in cleanroomomgevingen. Een van de grootste risico’s in de farmaceutische industrie zijn branden of explosies en de daaruit voortvloeiende rookverontreiniging van productieruimten, met name cleanrooms. Bij brand ontstaan roetdeeltjes en andere residuen tijdens de zware rookvorming, die neerslaan op de apparatuur en de hele faciliteit. Deze brandresten moeten eerst vakkundig worden verwijderd voordat de daadwerkelijke brandschade kan worden hersteld.De daaropvolgende kwalificatie en validatie van de apparatuur kan leiden tot aanzienlijke operationele onderbrekingen van enkele maanden, zelfs in het geval van een kleine brand.Dit is fataal voor een farmaceutisch bedrijf in tijden van just-in-time productie. Medische producten mogen alleen worden vervaardigd in gecertificeerde productiefaciliteiten en de faciliteiten vereisen toestemming van een nationale toezichthoudende instantie. Hercertificering na een brand in productieruimten is een langdurig proces.
Het belang van brandrook en brandbijproducten wordt vaak onderschat. Bij brand vormt rook het grootste gevaar voor mensen, omdat het moeilijk is om snel en veilig te evacueren. Daarnaast produceert rook brandbijproducten met corrosieve eigenschappen die aanzienlijke schade kunnen veroorzaken aan gebouwen, systemen en inventaris. De vervuiling kan resulteren in opruimkosten die de financiële schade veroorzaakt door de primaire brandschade ver overstijgen. En dan hebben we het nog niet eens over de daaruit voortvloeiende kosten door operationele stilstand.
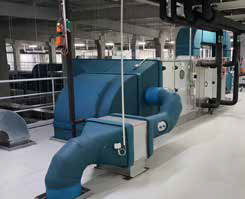
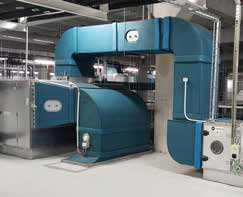
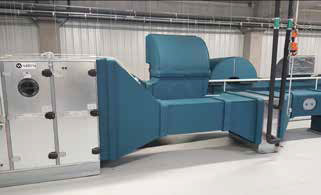
Grotere brandveiligheid met ArmaFlex Ultima
Naast brandgedrag is rookontwikkeling daarom een doorslaggevende factor bij de keuze van bouwmaterialen. Op basis van de gepatenteerde ArmaPrene™ technologie is ArmaFlex Ultima het eerste flexibele technische isolatiemateriaal met brandklasse BL-s1,d0. De ArmaPrene technologie biedt de hoogste brandbeschermingsstandaard op het gebied van flexibele isolatiematerialen.
Hoewel standaard elastomeerproducten met broomhoudende vlamvertragers de brandbaarheid bij brand effectief tegengaan, hebben ze de neiging om veel rook te produceren. De ArmaPrene technologie lost dit conflict op: door de ontwikkeling van intrinsiek vlamvertragende polymeren en het gebruik van ablatieve beschermende additieven kan de toevoeging van broomhoudende vlamvertragers volledig achterwege blijven. ArmaFlex Ultima produceert 10 keer minder rook dan een standaard elastomeerproduct.
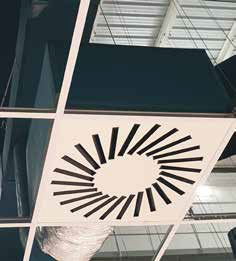
Volgens de Portugese bouwvoorschriften voor brandbeveiliging in gebouwen (Decreto-Lei n.º 220/2008 – Segurança Contra Incêndio em Edifícios) moeten thermische isolatiematerialen in luchtdistributiekanalen ten minste brandklasse B-s2,d0 bereiken. Als BL-s1,d0 geclassificeerd product voldoet ArmaFlex Ultima niet alleen aan de eisen, maar overtreft deze zelfs op lineaire kanalen.
Eenvoudige installatie
Alle luchtkanalen en andere systeemcomponenten in de nieuwe fabriek in Labesfal werden geïsoleerd met ArmaFlex Ultima. Om condensvorming en energieverlies te voorkomen, werden de koude luchttoevoerkanalen beschermd met 32 mm dikke platen. Voor de warme afvoerluchtkanalen werden ArmaFlex Ultima platen met een dikte van 19 mm gebruikt. In totaal gebruikte het isolatiebedrijf Martins Oliveira 3.800 m² ArmaFlex Ultima-platen. Terwijl ronde kanalen werden geïsoleerd met standaardplaten en aangebracht met ArmaFlex Ultima 700 lijm, gebruikte Martins Oliveira zelfklevende platen voor rechthoekige kanalen om de hoeveelheid lijm te verminderen en de installatie te versnellen. De isolatiematerialen en ArmaFlex Ultima 700-lijm werden geleverd door Distriplac Portugal – Comércio de Isolamentos. De installatie werd in 2022 in gebruik genomen.