Bij het horen van het woord “isoleren” wordt vaak in de eerste plaats gedacht aan energiebesparing. Energiebesparing is belangrijk en helpt om de klimaatdoelstellingen te realiseren. Maar in de industrie spelen ook andere factoren een rol. Bij Bunge Loders Croklaan, een producent van plantaardige oliën en vetten voor de voedingsindustrie, zijn diverse filters en deksels geïsoleerd, niet in de eerste plaats om energie te besparen, maar vanwege de persoonlijke veiligheid van medewerkers en contractors die werkzaamheden verrichten in de nabijheid van hete procesinstallaties.
Dirk Mulder is werkzaam bij Bunge Loders Croklaan op de Maasvlakte en vertelde dat de eerste aanleiding om te gaan isoleren voortkwam uit een voorstel om de werkomstandigheden te verbeteren. Het voorstel was om de ruimte beter te ventileren door meer buitenlucht toe te laten via extra ventilatieopeningen. Daarmee werd de oorzaak, namelijk warmte van de filters niet aangepakt. De oorzaak voor de hoge temperaturen in de ruimte met zogenaamde “vertical leaf filters” (VLF) was de warmte die van die filters afkomstig is. De filters waren ±1mtr aan de bovenkant niet geïsoleerd en konden aan het oppervlak opwarmen tot ca. 100 °C. In plaats van meer te ventileren is gekozen voor het isoleren van de filters.
Omdat er gewerkt wordt met plantaardige oliën en omdat de filters bestaan uit meerdere delen waarbij veel manuele handelingen nodig zijn lag het isoleren met de gebruikelijke systemen en materialen niet voor de hand. Toch kon er een materiaal gevonden worden dat geschikt was en aangebracht kon worden op de filters. Het gaat om een isolatiemateriaal van rubber dat bestand is tegen de componenten uit de oliën en dat geschikt is voor lastig te isoleren oppervlakken. Chabel levert en monteert dit isolatiemateriaal en is nauw betrokken bij de toepassing ervan.
Bunge Loders Croklaan heeft zelf uitgezocht hoe en waar het materiaal diende te worden aangebracht en op basis van verschillende testen is samen met Chabel gekozen voor een bepaalde materiaalsamenstelling. Inmiddels zijn op de Maasvlakte verschillende filters (in totaal zo’n 44 filters), leidingwerk en de deksels van hoge druk stoomketels voorzien van isolatie op een zodanige wijze dat het oppervlak minder warm wordt dan 60 °C.
Binnen de CINI norm (Commissie Isolatie Nederlandse Industrie) voor isolatie is met name gekeken naar het onderdeel “personal protection” en op basis hiervan zijn plekken met een temperatuur hoger dan 60 °C geïsoleerd. Dit resulteert in een veiligere werkomgeving en een beter klimaat om in te werken.
Het reinigen van de isolatie is eenvoudig uit te voeren met warm water, mits er niet met hoge drukspuiten op het materiaal wordt gespoten. Verder is er bij de installaties die in bedrijf zijn met deze isolatie geen behoefte aan onderhoud door de leverancier. Eventuele beschadigingen kunnen gemakkelijk hersteld worden door de beschadiging af te smeren met vers component.
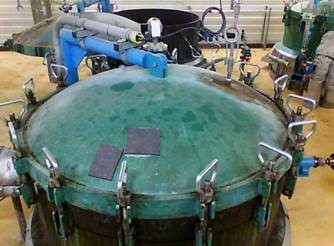
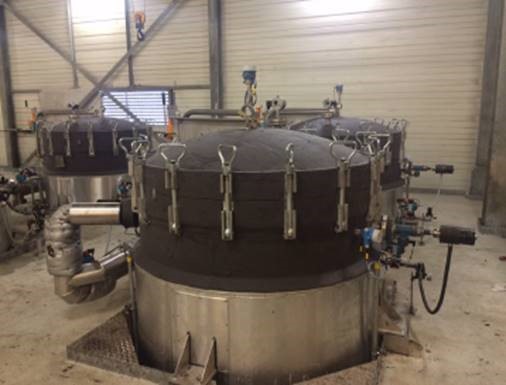
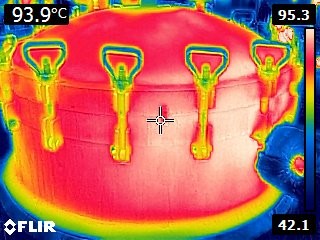
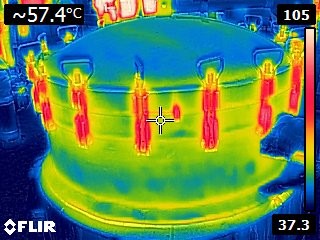
Bijkomend voordeel is uiteraard de energiebesparing. Per VLF-filter bedraagt die ca. 3 kW continu en bij de energieprijzen van eind 2020 komt de terugverdientijd op ca. 2,5 jaar uit.
De firma Chabel, die de isolatie heeft aangebracht bij Bunge Loders Croklaan, maakt duidelijk dat de isolatie in overleg met de opdrachtgever is aangebracht. Door in de ruimte de VLF-filters te isoleren is het werkklimaat aanzienlijk verbeterd en was de uitbreiding op ventilatieopeningen niet meer nodig.
Bunge Loders Croklaan heeft gedurende de voorbereiding, het ontwerp en het aanbrengen van de isolatie steeds meegedacht en samengewerkt met Chabel.
Het is zeker niet zo dat alle bedrijven zo nauw betrokken zijn bij het isoleren van installaties als Bunge Loders Croklaan. Bij veel bedrijven wordt de isolatie overgelaten aan het isolatiebedrijf en wordt meestal op prijs geselecteerd. Door als opdrachtgever bij het aanvragen en beoordelen van offertes niet alleen op de prijs te letten kan de prestatie van de isolatie verder verbeteren.
De besparingen voor isolatie van filters zijn hieronder in een algemeen voorbeeld toegelicht.
Chabel heeft voor een filter met een diameter van 1500 mm uitgerekend wat het kost om te isoleren:
Bij de toegepaste isolatie bedragen de kosten ca. € 2400 inclusief montage. De terugverdientijd bij een temperatuur aan het oppervlak van het filter (zonder isolatie) van 110 °C en een aardgasprijs van € 0,25/Nm3 bedraagt ca. 1,5 jaar.
In de kosten voor het aardgas zijn geen kosten doorberekend voor CO2, als die wel meegenomen worden zal de terugverdientijd korter zijn.
In 2014 heeft Epro Consult in opdracht van de ketenorganisatie MVO en met ondersteuning van de Rijksdienst voor Ondernemend Nederland (RVO) een workshop georganiseerd waarop Chabel een toelichting heeft gegeven op de toepassingsmogelijkheden van de door hen toegepaste isolatie. Bedrijven uit de margarine-, vetten- en oliënindustrie (MVO) konden daar kennis nemen van het isolatiemateriaal. Dit materiaal van Chabel is met name geschikt voor lastig te isoleren oppervlakken zoals filters en heeft als voordeel dat er geen aantasting door de gebruikte oliën plaatsvindt en er ook geen olie door het materiaal wordt opgenomen.
Sinds 2014 is deze isolatie bij diverse bedrijven in de eetbare olie industrie toegepast en inmiddels ook in de petrochemie. De nieuwe generatie van het materiaal is verder ontwikkeld en is ook onbrandbaar.