Colpro Technical Solutions, onderdeel van Colpro ontwikkelt, produceert en monteert voor diverse toepassingen zoals klimaatkamers, cleanrooms, droogkamers en besturingssystemen. Eind vorig jaar hebben ze bij van Geenen B.V. een nieuwe cleanroom gebouwd. Deze cleanroom met een oppervlakte van ruim 200m2 is voorzien van de nieuwste technieken en een uiterst moderne luchtbehandelingsinstallatie.
Hoe zijn jullie bij dit project terechtgekomen?
”Wij werken al lange tijd samen met Van Geenen”, vertelt Marcel Vreeling Sales Manager bij ColPro Technical Solutions b.v. “Dit bedrijf is gespecialiseerd in het slijpen en polijsten van materialen zoals roestvrij staal en titanium. Ze leveren onder andere aan grote spelers als ASML, Boeing en Airbus. Onze samenwerking gaat al tientallen jaren terug, en toen zij een nieuwe cleanroom nodig hadden, hebben ze ons benaderd. Omdat we al eerder cleanrooms en technische oplossingen voor hen hebben geleverd, wisten zij dat wij de expertise en ervaring in huis hadden om aan hun strenge eisen te voldoen.”
Wat hield het project precies in?
“Het ging om de bouw van een 200 vierkante meter grote cleanroom. Van Geenen had een ruimte nodig waarin geslepen en gepolijste materialen volledig stofvrij verpakt konden worden. Deze cleanroom moest voldoen aan strikte eisen op het gebied van luchtkwaliteit, temperatuur en vochtigheid om de kwaliteit van de materialen te waarborgen.”
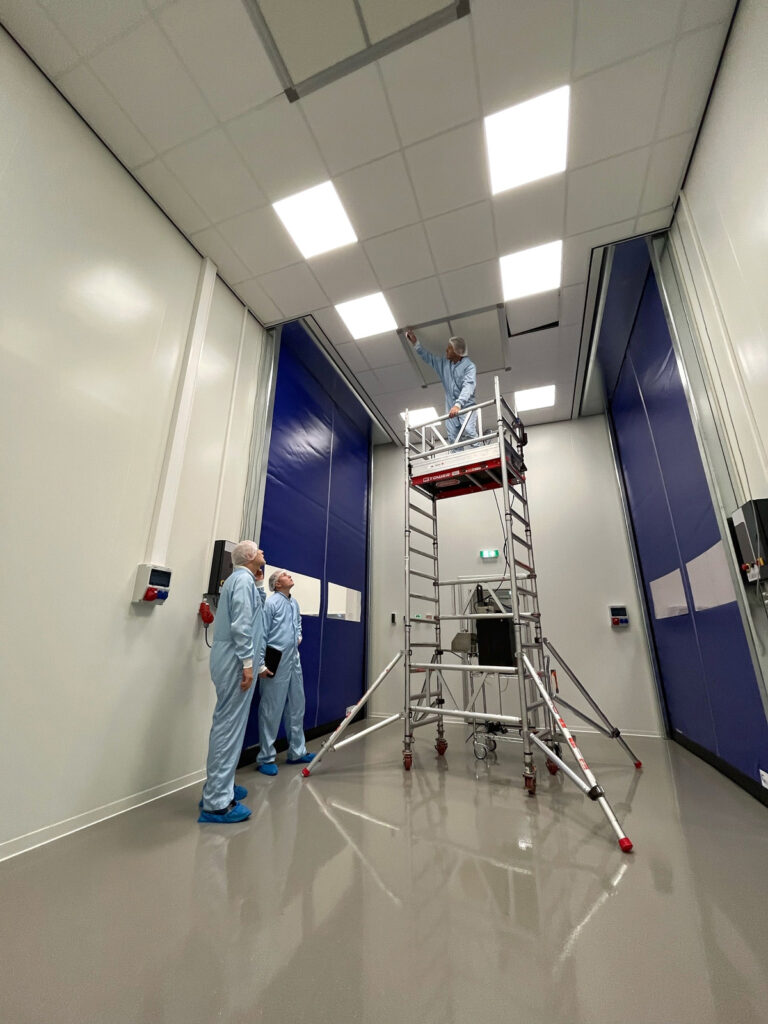
Hoe hebben jullie het project aangepakt?
“We starten met het verzamelen van de specificaties van de klant. Vervolgens gaat het project naar onze tekenkamer, waar alles wordt geëngineerd. Hier worden onder andere de uitslagen voor de sandwichpanelen met isolatie gemaakt. Daarnaast wordt er gekeken naar technische installaties, zoals verlichting, luchtregulatie en klimaatbeheersing. Na de engineeringfase gaan we over tot productie in onze fabriek, waarna onze monteurs de cleanroom op locatie opbouwen. Tijdens dit proces werken we nauw samen met de klant om eventuele aanpassingen of verbeteringen direct te kunnen implementeren. We maken hiervoor een gedetailleerde planning waarin de werkzaamheden per fase worden afgestemd. Waarbij elk onderdeel afzonderlijk wordt getest voordat de volgende fase begint.” Regelmatige bouwvergaderingen helpen volgens Vreeling bij het voorkomen van knelpunten en zorgen ervoor dat elke partij op de hoogte blijft van de voortgang. “Deze samenwerking heeft ervoor gezorgd dat alle systemen correct geïnstalleerd en geïsoleerd zijn, waardoor de cleanroom voldoet aan de gestelde eisen.”
Hoe verliep de samenwerking tussen de installateur en de isolatiebedrijven?
“De samenwerking tussen de installateur en de isolatiebedrijven was een cruciaal aspect van het project. Wij werken vaak met vaste installateurs en isolatiebedrijven die gewend zijn aan onze werkwijze. De installateur is verantwoordelijk voor de technische installatie, zoals luchtbehandeling, elektriciteit en klimaatbeheersing. De isolatiebedrijven zorgen voor de thermische en akoestische isolatie van de technische installaties en de luchtkanalen. Dit vereist een strakke coördinatie, omdat bepaalde werkzaamheden op elkaar afgestemd moeten worden. Zo moet de installatie van luchtkanalen en leidingwerk plaatsvinden voordat de isoleerders hun werkzaamheden kunnen afronden. Waarna de isolatiebedrijven aan de slag kunnen met het aanbrengen van de juiste isolatiematerialen op de luchtkanalen en leidingwerk om warmteverlies en condensatie te voorkomen.”
Was er een programma van eisen waar de isolatie aan moest voldoen?
Cleanrooms hebben strikte eisen op het gebied van luchtkwaliteit. “De cleanroom die wij voor Van Geenen hebben gebouwd, voldoet aan ISO-klasse 6”, licht Vreeling toe. “Dit betekent dat het aantal stofdeeltjes per kubieke meter lucht tot een minimum beperkt moet worden. Daarnaast moesten de temperatuur en vochtigheid nauwkeurig gecontroleerd worden. Voor de luchtzuivering hebben we gebruikgemaakt van geavanceerde filtersystemen die continu de lucht reinigen. Verder is er rekening gehouden met luchtdrukregulatie, zodat er een gecontroleerde luchtstroom in en uit de cleanroom plaatsvindt.”
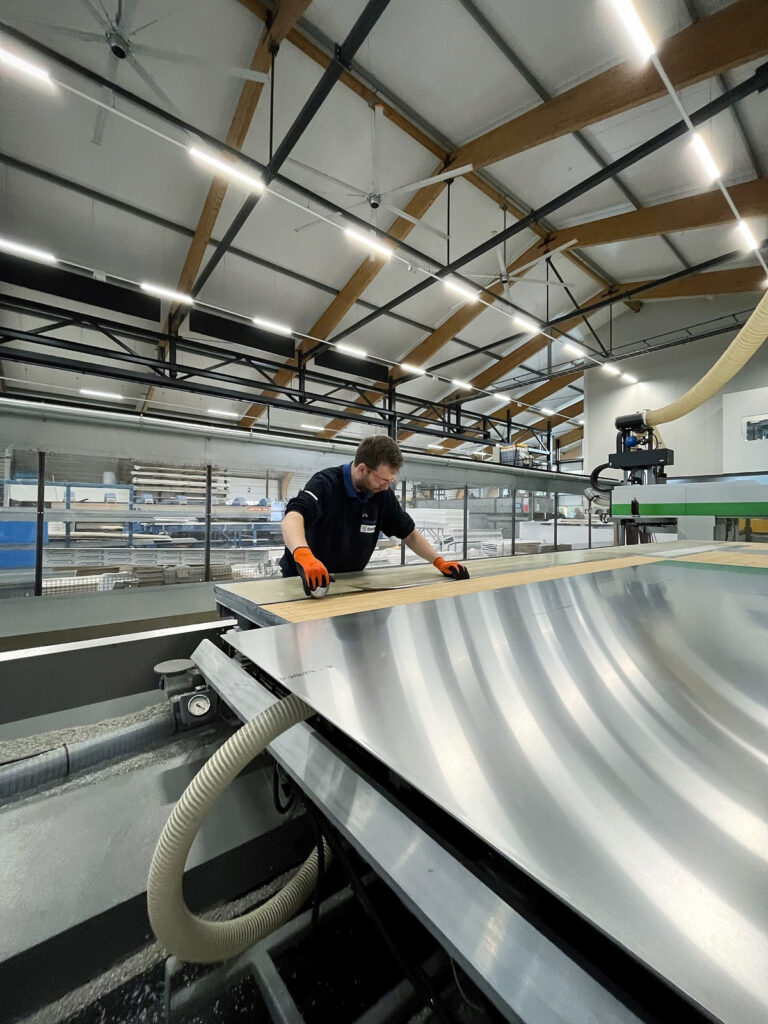
Welke materialen hebben jullie toegepast?
“Voor de panelen van de cleanroom hebben we gebruikgemaakt van sandwichpanelen met een EPS-isolatiekern. Daarnaast hebben we gelakte staalplaten gebruikt voor de afwerking. De luchtkanalen zijn geïsoleerd met steenwol en afgewerkt met aluminium beplating. In de technische ruimte zijn de koelleidingen geïsoleerd met Armaflex, warmteleidingen met steenwol en afgewerkt met aluminium beplating en de appendages met matrassen.”
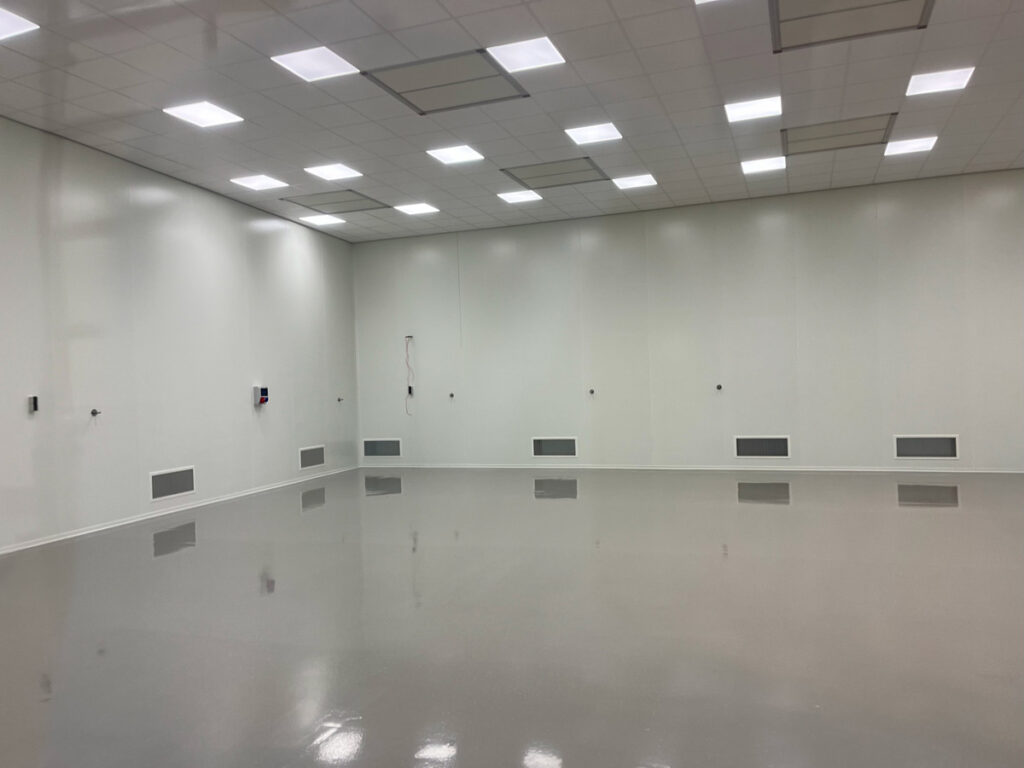
Beschikken jullie over een eigen werkplaats om de materialen op maat te snijden en te verwerken?
Een belangrijk onderdeel van de productie is de eigen werkplaats, waar materialen volledig op maat worden gesneden en verwerkt. Door gebruik te maken van geavanceerde machines, kunnen we complexe precisiebewerkingen uitvoeren, zoals het snijden en lamineren van panelen en het vervaardigen van complexe metalen profielen. “Dit stelt ons in staat om klantspecifiek maatwerk te leveren en snel in te spelen op projectbehoeften.” Om de kwaliteit en efficiëntie verder te optimaliseren, heeft Colpro gekozen voor de JÖRG Lasersnijmachine. Deze machine snijdt direct vanaf coil, wat niet alleen zorgt voor een efficiënter proces, maar ook voorkomt dat het plaatmateriaal beschadigt. “Dit innovatieve systeem biedt meer vrijheid in ontwerp en productie, waardoor Colpro nog creatiever kan werken aan de sandwichpanelen. Doorslaggevend was dat de JÖRG snijdt vanaf coil en omdat de plaat zowel aan de bovenzijde als aan de onderzijde niet beschadigt door de kunststofrollen.”
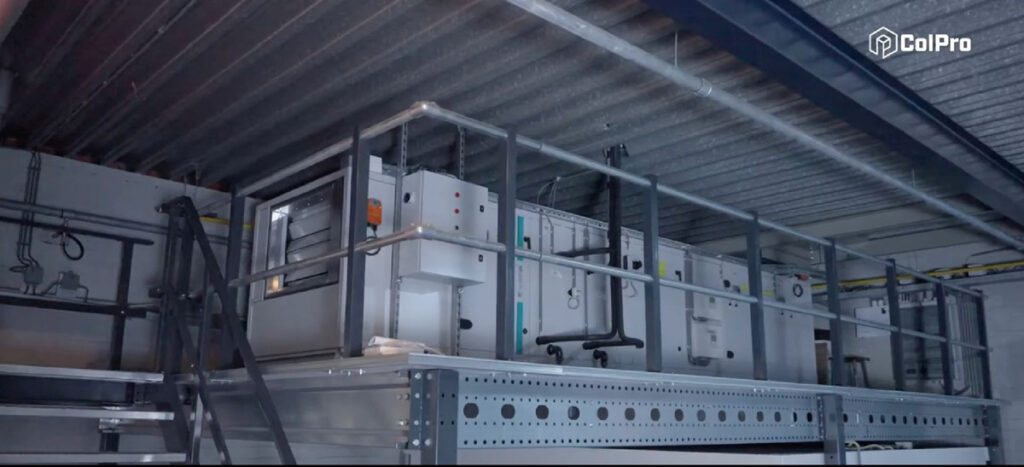
Hoe lang hebben jullie over het project gedaan en met hoeveel mensen?
“De productiefase duurde ongeveer 16 weken. Daarna volgde de montage op locatie, wat enkele weken in beslag nam. In totaal werkten ongeveer 10 tot 15 mensen aan het project, inclusief engineers, productiemedewerkers en monteurs. Tijdens de bouw waren er ook regelmatige kwaliteitscontroles om ervoor te zorgen dat alles volgens de specificaties werd uitgevoerd. Dit hielp ons om eventuele uitdagingen direct aan te pakken en de efficiëntie te waarborgen. De montage is uitgevoerd door onze eigen monteurs. Omdat alle onderdelen in onze fabriek zijn geproduceerd, konden we de cleanroom snel en efficiënt op locatie opbouwen. We maken veel gebruik van prefab materialen, zoals voorgefabriceerde sandwichpanelen en prefab luchtkanalen, zodat de montage sneller verloopt.”
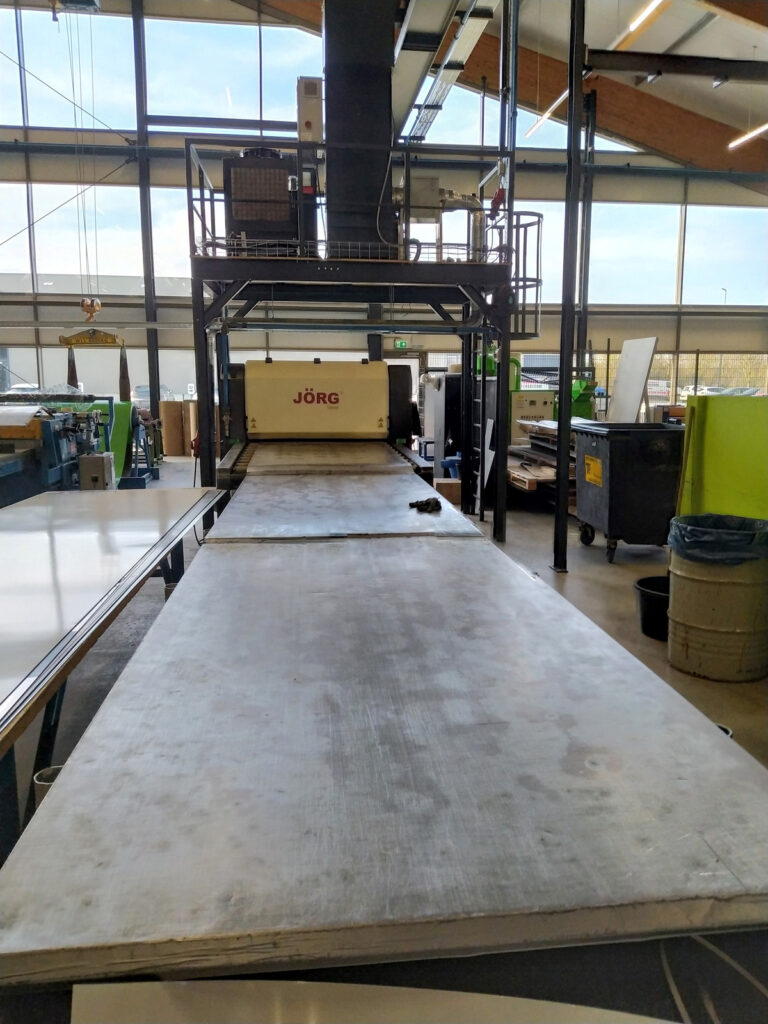
Hoe kijken jullie terug op het resultaat?
“Wij zijn zeer tevreden met het eindresultaat. De cleanroom voldoet volledig aan de gestelde eisen en is inmiddels operationeel. De samenwerking met Van Geenen verliep uitstekend, en we hopen in de toekomst meer van dit soort projecten met hen te realiseren. Van Geenen heeft aangegeven dat de cleanroom een enorme verbetering is ten opzichte van hun eerdere faciliteiten, vooral op het gebied van luchtkwaliteit en werkcomfort.”
Wat zijn jullie toekomstplannen?
“Wij blijven ons focussen op maatwerk en innovatie. We willen onze expertise op het gebied van cleanrooms en klimaatkamers verder uitbreiden. Daarnaast blijven we investeren in nieuwe productietechnieken en samenwerkingen met gespecialiseerde partners om onze klanten nog beter van dienst te zijn.”
Tekst: Loet van Bergen en Foto’s Van Geenen